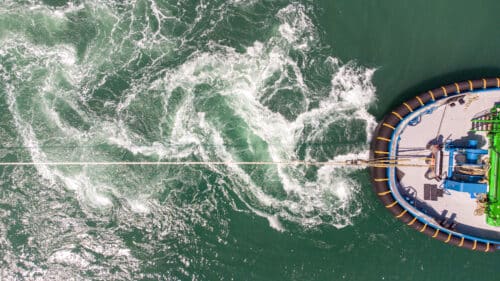
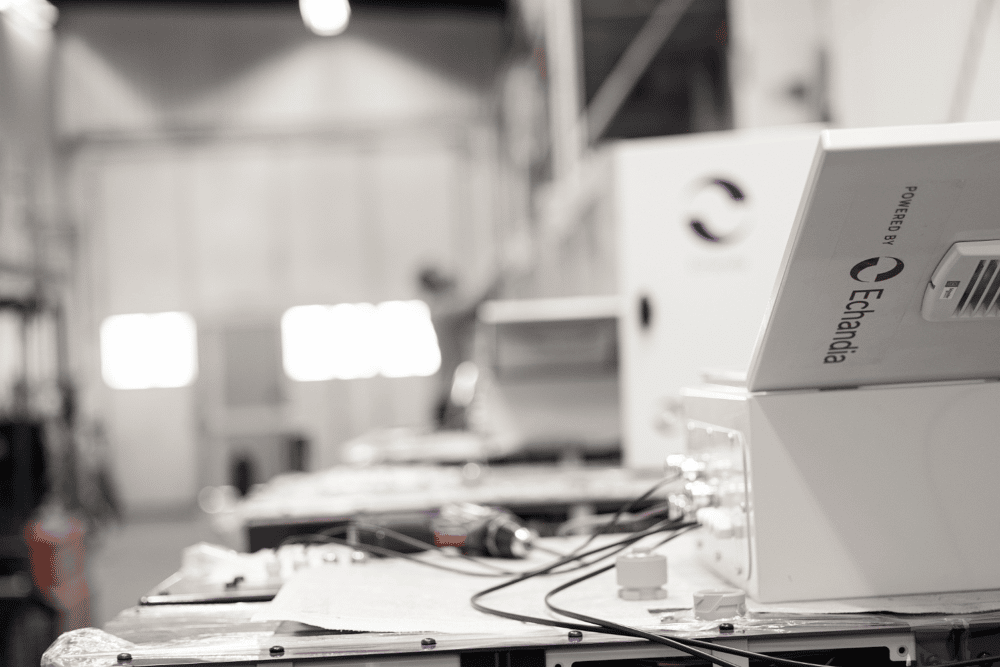
What’s the role of the BMS in a maritime battery system?
- Insights
- 12 October 2022
All battery systems rely on a battery management system – the BMS to function in the way we expect. In fact, the BMS is a vital part in creating safe and durable systems that can sustain the entire life span without premature degradation or failures.
BMS also has role to play in battery safety. A holistic view on safety means taking measures in all areas to ensure the stability and durability of the system in all types of situations. That means having a safety perspective from the cell level to the software, hardware, and the system as a whole,
In the current setup, the Echandia BMS and its functionality is located in cabinet separated from the battery strings as shown below.
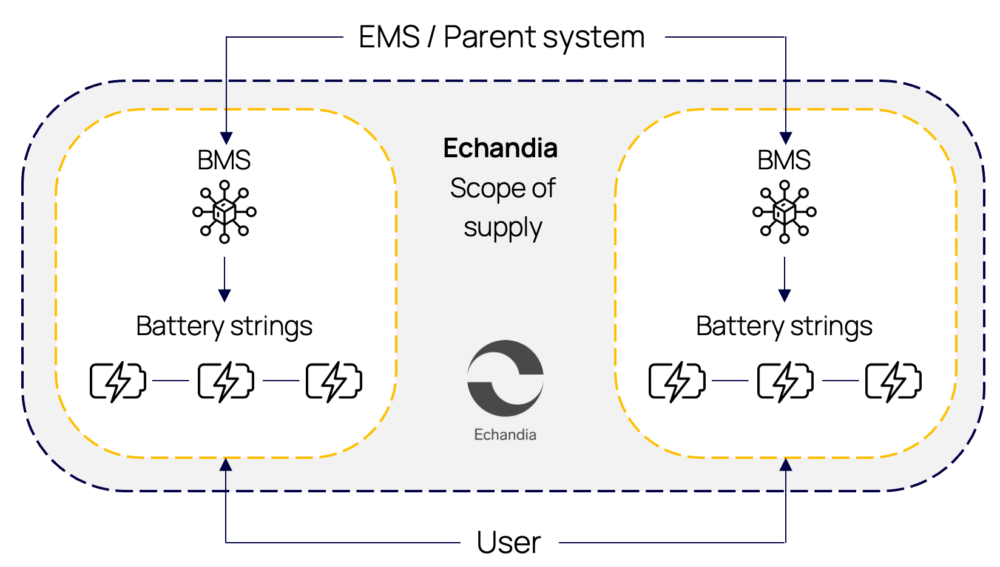
Control of the Energy Storage System
In this article we will go through the basics of the battery management system and what role it has in maritime battery system:
- What is a BMS?
- Why is the BMS important?
- What does the BMS do?
What is a battery management system (BMS)?
If the battery cell is the DNA that sets the theoretical limits for the performance of the battery, and the battery modules are the muscles to dispel power and store energy – the BMS is where the intelligence lie – in keeping with the analogy of the human body – it is the brain.
Just like computers, a battery system is equal parts hardware and software. Much of the capabilities and functionality of the hardware, and how it interfaces with other systems and humans, lies in the BMS.
Its role is to optimize how the battery system functions and to make sure it is safe and running as it should. To do so, it gathers all the available operational data such as battery voltage levels, temperatures, capacity, state of charge (SoC) and state of health (SoH) and provides this to the operator as well as other integrated systems.
What does the BMS do?
So, what are the main functions for a battery management system in a marine application. Without the BMS, the battery system would be a non-functional piece of hardware unable to operate in the complex and challenging environments that it is set to do.
Making sure the battery is functioning safely is the most important role of the BMS in a battery energy storage solution (BESS). It monitors, everything that goes on in and around the cells, modules and casing (racks) and alarms, and prevents anything that exceeds safe operating levels. This will mitigate many harmful or potentially disastrous events that otherwise could have occurred.
To simplify, the BMS has four overall functions
- electrical management and safety protection
- thermal management and safety protection
- capacity management
- diagnostics and data collection
BMS and electrical management
The main purpose of electrical management is to ensure that the battery pack operates within its electrical safe operating area (SOA), meaning in practice to keep the battery within its voltage and current limitations.
The BMS is built and programmed to optimize these levels to protect the battery. Protecting the battery system from abuse and overly aggressive usage ensures that the planned life span is reached, while at the same time making sure the application doesn’t encounter sudden failure or stops working.
Examples of Echandia BMS functionality for electrical management
- Cell voltage monitoring in individual cells and all modules
- Current monitoring, to not exceed 160A (or 3.5C) with the intention to protect electrical installation
- Alarm if any cell voltage exceeds 2.7V – at 2,8V the string will disconnect regardless.
- De rating charging/discharging strategy that transmit maximum allowable current to the PMS
BMS and thermal management
The BMS will warn if the temperature reaches 45° in any module and request the strings to disconnect at 55° to protect the lifespan of the battery.
The LTO battery cell can operate well under a wide temperature range (approximately -20° –– 60°) and is extremely resilient in both cold and warm outside temperatures. As a rule of thumb though, most batteries react negatively when exposed to excess cold or heat with increased speed of degradation and reduced capacity as a result.
Apart from monitoring temperatures, the BMS controls cooling or heating systems. Cooling can be done with air flow through the racks and modules or with forced convection cooling. Battery management systems control temperatures to minimize battery degradation. Running warm for too long or charging in cold weather is extremely bad for most battery cells (LTO being an exception) and might need excessive cooling (liquid cooling) or systems for pre-heating cold batteries before charging.
Examples of Echandia BMS functionality for thermal management
- Temperature monitoring of the battery cells and ambient locations within every module
- Alarm goes off if any module temperature exceeds 45°C.
- Fault signalling and interruption of the charging current if any module temperature exceeds 55°C.
BMS and capacity management
The third area for the BMS is capacity management, which ultimately optimizes performance of the battery by balancing voltage and SOC between cells. Without proper capacity management, the battery system would quickly become non-functional.
- Advanced state-of-charge (SOC) algorithm that accurately computes the SOC even during charge and discharge and transmits the SOC value to the PMS.
- Balancing features that adjust the voltage of the cells so that all cells in the pack are kept within a small range of each other (cells are said to be “balanced”)
BMS – diagnostics and data collection
The BMS collects all data and events that is rendered by the system, which can be used to analyze the system performance as well as for long term optimization of the system design and warranty purposes. The BMS can be configured with different layers and levels of user access, to avoid unauthorized use of the system.
The internal operating parameters of the Echandia system are stored in the BMS. Logged data can either be retrieved on demand or automatically through Echandia Cloud Analysis. The Echandia BMS communicates key data and performance parameters to the PMS (power management system) and can be logged by the PMS remote diagnostics system and transferred to the cloud for further analysis.
Examples of data collected to be analyzed:
- Charge and discharge currents
- SoC in percentage points (string level)
- Cell voltages
- Cell temperatures (max – min)
BMS integration
A non-negligible function of the BMS is how well it can communicate with other systems. If you think of the BMS as the brain, communicating with other parts of the system becomes vital. A flexible BMS allow for easy integration with the parent system and provides several communication protocols that can be used simultaneously. The most common ones are CANbus 2.0, CANbus J1939, Modbus/TCP, Profinet are protocols that can be used for the BMS integration.
Below is a short list of the most common protocols available:
CAN bus Communication
The CAN bus protocol has been widely used in the automotive industry and allows the BMS to exchange messages with the parent system by simple wiring. When used in a network A CAN filter can be implemented allowing the BMS to receive only the messages addressed to it, and thereby reducing the risk of network congestion.
Modbus/TCP Communication
The Modbus/TCP server allows the BMS to receive commands from EMS/parent system. The EMS/parent system can read operational values and send commands to the BMS. There can also be a second Modbus/TCP server that allows a secondary EMS/parent system to read the operational values from the BMS
Profinet Communication
By using Profinet when communicating with the parent system, the BMS becomes adaptable and flexible. A ring network with fiberoptics cabling the BMS can be set with a customized DNS and IP-address, adapting to the hardware configuration of the customer network.
Other interfaces
Apart from these, other external sensors and systems can also be integrated to the BMS if needed, for instance:
- Integration with gas sensors and water leakage sensors
- Insulation monitoring devices (IMD)
- External cooling systems, i.e., in the battery compartment
- Integration with external fire suppression system
Critical safety features in the BMS
As previously mentioned, most failure modes are detected and protected against by the BMS.
A key functionality of the BMS then, is to warn, alarm and eventually disconnect the system. Any non-typical behaviour results in a warning, that may set off an alarm later, if the problem persists. In case a normal disconnection of the string is successful, the system will return to normal operation after restarting the string. If not, there will be an emergency disconnect.
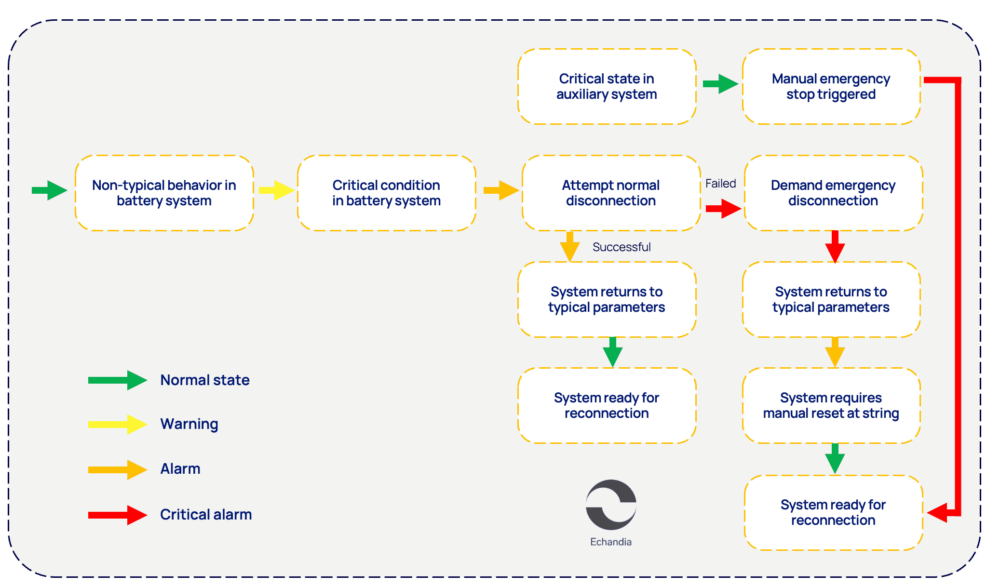
Flowchart for emergency disconnection
In the case of unforeseen and unpredictable events, we rely on inherent cell level safety as this table shows.
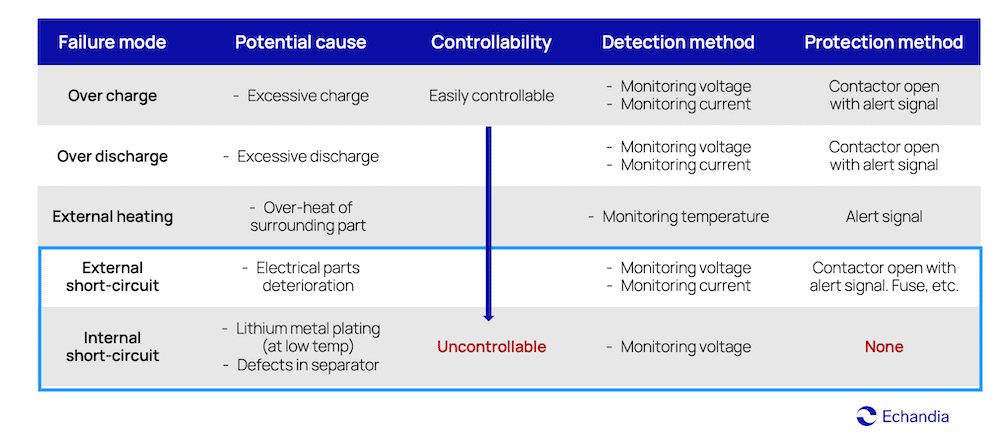
The BMS handles controllable failure modes by detecting and protecting the battery system. Internal short circuiting cannot be easily protected against and comes down to cell characteristics.
Summary
The BMS is the brain of the battery system, and is a vital part to create a safe, durable and stable system. As battery systems grow bigger in size, the role of the BMS becomes even more crucial. With larger systems there are more data to handle, and the pace in which it is processed is increasing.
To better understand Echandias BMS design, contact our team to set up a tech meeting.
Contact us